Enhancing Industry Standards with Precise Injection Mould Supply
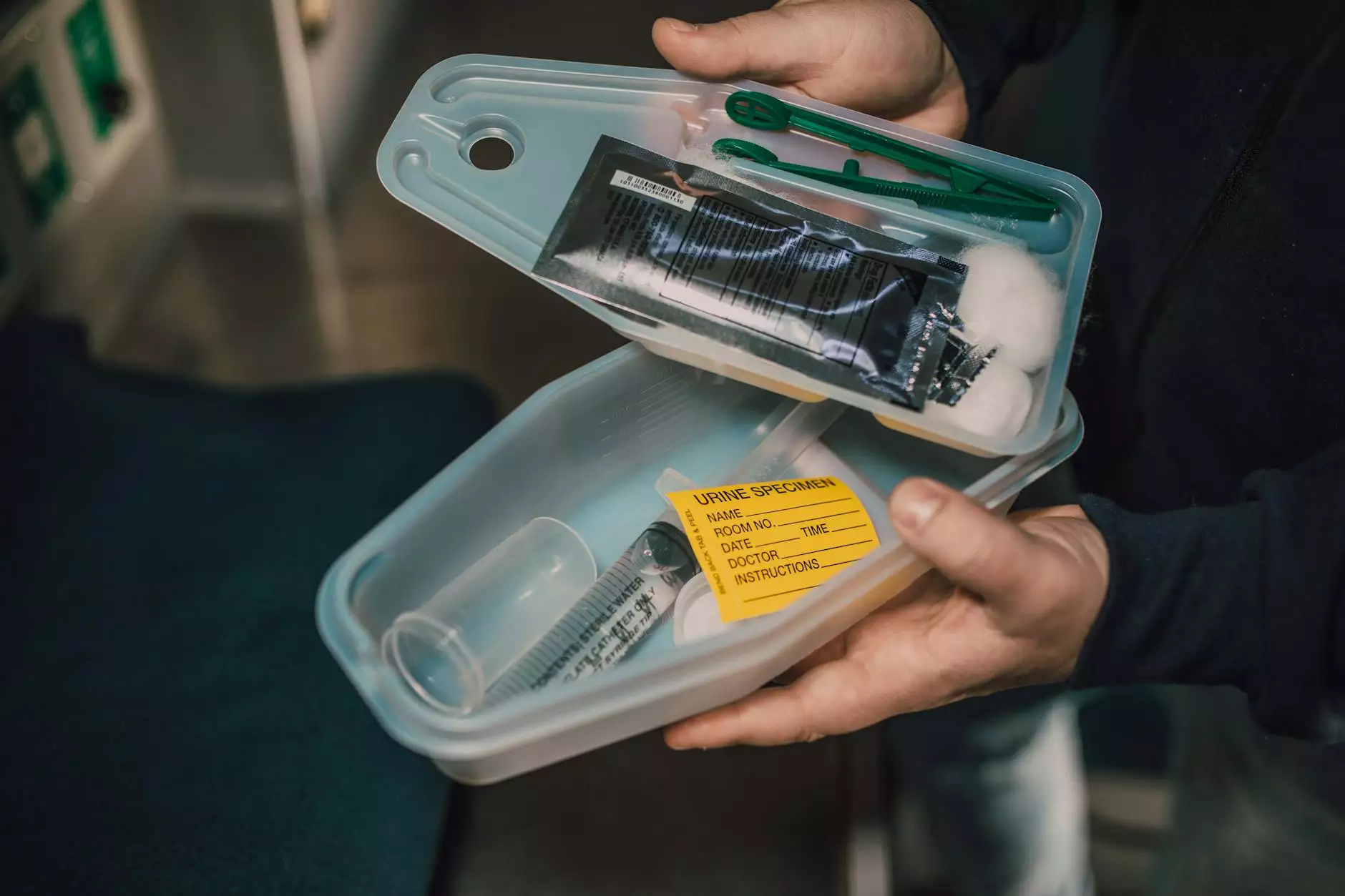
In today's hyper-competitive manufacturing landscape, precision and efficiency are not just goals but essential attributes that define success. The metal fabrication sector stands at the forefront of this evolution, with precise injection mould supply playing a pivotal role in driving innovation and quality at every stage of production. This article delves deep into the elements that make injection moulding a vital component of modern industrial processes, particularly within the realm of metal fabrication.
The Importance of Injection Moulding in Metal Fabrication
Injection moulding is a manufacturing process that allows for the creation of complex shapes and parts with incredible detail and efficiency. In the context of metal fabrication, this process is crucial for producing components that meet stringent industry standards. Here are several reasons why precise injection mould supply is imperative:
- Efficiency: Injection moulding significantly reduces production time while increasing output.
- Cost-Effectiveness: High-volume production reduces the cost per unit, making it more viable for businesses.
- High Precision: The process is known for its dimensional accuracy, which is essential in industries requiring tight tolerances.
- Material Versatility: A wide range of materials can be used, offering flexibility in design and function.
- Sustainability: The efficiency of the process leads to less waste, supporting eco-friendly practices.
Understanding Precise Injection Mould Supply
A precise injection mould supply involves not just the physical delivery of moulds but also the incorporation of advanced technologies and high-quality materials. This ensures that every piece manufactured meets the required specifications and performs reliably in its intended application.
Key Elements of Quality Injection Mould Supply
When it comes to the injection mould supply process, several factors dictate quality:
1. Design and Engineering
Effective mould design is crucial. It requires a thorough understanding of the part geometry, material behavior, and cooling requirements. Expert engineers utilize CAD (Computer-Aided Design) and CAE (Computer-Aided Engineering) tools to create moulds that are optimized for production.
2. Material Selection
The choice of materials for both the mould and the components produced can greatly impact the final product’s performance. Strong, durable materials tend to yield longer-lasting, reliable parts, which are essential for industries such as automotive, aerospace, and medical.
3. Manufacturing Process
The manufacturing techniques utilized in producing moulds can vary. Techniques like 3D printing for rapid prototyping, CNC machining for precision work, and EDM (Electrical Discharge Machining) for intricate designs can enhance the quality and precision of moulds dramatically.
4. Quality Control Measures
Consistent quality checks throughout the production process are vital. This can include dimensional accuracy tests, material inspections, and functionality evaluations to ensure that the moulds meet all necessary specifications before they are put into operation.
Technological Advancements in Injection Moulding
The field of injection moulding has seen tremendous advancements over the years. Innovations in technology have not only improved the production process but have also elevated the standards of precision required in today’s manufacturing environments. Here are some notable advancements:
- Smart Moulding Technology: Using IoT (Internet of Things) devices, manufacturers can now monitor mould performance in real-time, leading to enhanced efficiency and minimized downtime.
- Energy Efficiency: Modern moulding machines are increasingly energy-efficient, reducing operational costs and contributing to sustainable practices.
- Automated Systems: Automation in injection moulding reduces human error and enhances the accuracy and speed of production processes.
- Simulation Software: Advanced simulation software allows for better prediction of material flow and cooling processes, helping in optimizing design and reducing the time for development.
The Benefits of Partnering with a Reliable Injection Mould Supplier
Choosing the right partner for precise injection mould supply is crucial for any business in the metal fabrication industry. Here’s how a reliable supplier can help enhance your operations:
1. Quality Assurance
Partners with a solid reputation in the industry often have established quality assurance protocols in place, ensuring that all moulds produced meet the highest standards.
2. Technical Support
Innovative suppliers provide ongoing support, including design optimization advice, troubleshooting during production, and recommendations on best practices for maintenance.
3. Cost Efficiency
Suppliers who specialize in precise injection mould supply can provide insights into cost-saving measures through optimally designed moulds and efficient production practices.
4. Timely Delivery
A dependable supplier understands the importance of deadlines and thus ensures timely delivery of moulds, preventing delays in production schedules.
Case Studies in Successful Injection Moulding
Real-world examples help illustrate the impact of precise injection mould supply. Several leading companies have transformed their production lines through efficient injection moulding:
Case Study 1: Automotive Component Manufacturer
One of the leading automotive component manufacturers adopted advanced injection moulding technologies, reducing production times by 30% and drastically cutting down their material wastage. By collaborating with a specialized mould supplier, they managed to implement quality control measures that reduced defects by over 15%.
Case Study 2: Medical Device Manufacturer
A medical device manufacturer required high-precision components that met strict regulatory standards. Through precise mould design and the use of high-quality materials provided by their injection mould supplier, they not only achieved compliance but also improved their production efficiency, resulting in a 20% reduction in costs.
Challenges in Injection Mould Supply and Solutions
Despite the many benefits, challenges exist in the process of injection mould supply. Here are a few common issues along with potential solutions:
1. Material Limitations
Some materials may be difficult to work with due to their properties. Solution: Working closely with suppliers who understand advanced material science can yield alternative solutions or advanced materials tailored to meet specific requirements.
2. High Initial Costs
Initial investment in quality moulds can be high. Solution: Consider structured payment plans or financing options offered by some suppliers to mitigate upfront costs.
3. Changing Design Needs
Modern products often require design changes throughout their lifecycle. Solution: Select a mould supplier capable of rapid prototyping and agile design changes to accommodate evolving market demands.
The Future of Injection Moulding in Metal Fabrication
As industries evolve and customer demands shift, the future of precise injection mould supply looks promising. We can expect continued advancements in:
- Biodegradable Materials: As sustainability becomes a key focus, the integration of eco-friendly materials into moulding processes will likely increase.
- Advanced Robotics: Automation will further streamline processes, increasing production speeds and reducing costs.
- Digital Twin Technology: This allows for the simulation and optimization of moulding processes in real-time, enhancing efficiency and reducing time to market.
Conclusion
In summary, the role of precise injection mould supply in the metal fabrication industry cannot be overstated. It is integral not just to manufacturing processes, but to the overall quality and efficiency of the products being developed. By focusing on technological advancements, choosing reliable partners, and staying abreast of industry trends, manufacturers can significantly enhance their competitive edge. For businesses seeking to thrive in this dynamic landscape, investing in high-quality injection moulding is not just an option—it's a necessity.
For more information about enhancing your manufacturing capabilities, visit Deep Mould, your trusted partner for precise injection mould supply in the metal fabrication sector.