Unlocking Innovation: A Deep Dive into the Cylinder Liner Factory
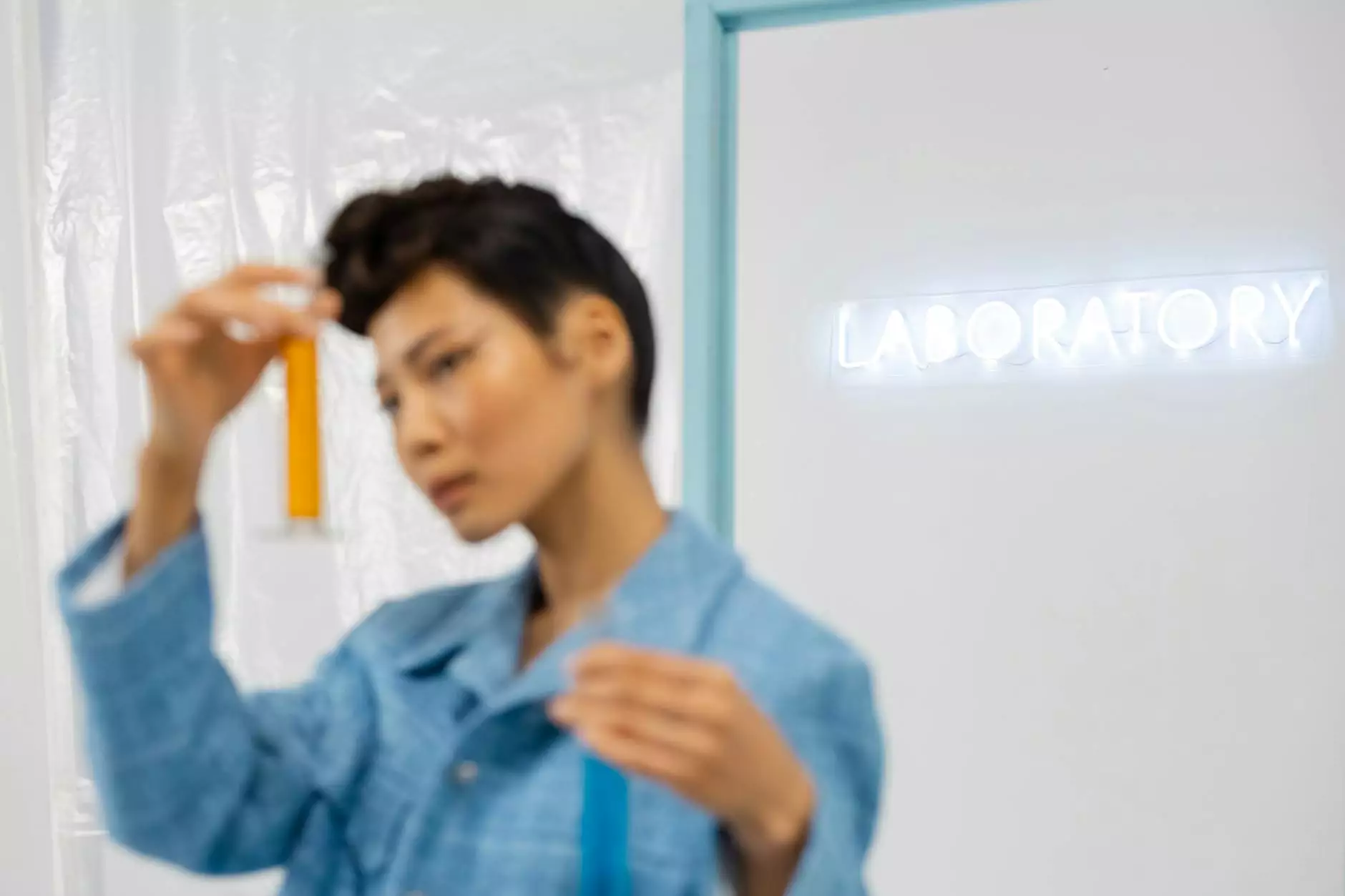
In the realm of diesel engine parts, the role of a reliable cylinder liner factory is pivotal. These factories serve as the bedrock for producing high-quality liners that contribute extensively to the efficiency and performance of diesel engines. This article will explore the intricate processes involved in manufacturing cylinder liners, the significance of quality in the engine performance, and how companies like client-diesel.com are at the forefront of this critical industry.
Understanding Cylinder Liners
Cylinder liners are components that provide a wear-resistant surface for the piston to slide within the cylinder. They are essential in supporting the combustion process and maintaining the structural integrity of the engine block. The quality of a cylinder liner significantly impacts:
- Engine Longevity: High-quality liners reduce wear and tear, extending the engine's lifespan.
- Performance Efficiency: Properly designed liners improve fuel efficiency and power output.
- Heat Dissipation: Liners play a critical role in managing engine heat, thus preventing overheating.
The Manufacturing Process of Cylinder Liners
The journey of creating a cylinder liner begins with the selection of the right materials. Typically, cylinder liners are made from cast iron or other alloys that can withstand high temperatures and pressures. The process can be broken down into several key stages:
1. Material Selection
The choice of materials is crucial, as it affects both the durability and the performance of the liner. Most cylinder liners are manufactured using:
- Gray Cast Iron: Known for its excellent wear resistance.
- Hypoeutectic Alloy: Offers improved thermal stability.
- Composite Materials: Used in specialized applications for weight reduction.
2. Molding Process
The molding process shapes the selected material into the desired cylinder liner form. This may involve:
- Casting: Pouring molten metal into molds to create the liner shape.
- Metal Injection Molding (MIM): A newer technique that allows for more complex geometries.
3. Machining
Post-molding, the liners undergo machining processes to achieve precise dimensions and surface finishes. Various techniques are employed, including:
- Turning: A process to produce cylindrical shapes.
- Grinding: Achieves smooth, precise surface finishes.
4. Surface Treatment
To enhance wear resistance and performance, cylinder liners are often subjected to surface treatments such as:
- Hardening: Increases durability.
- Ceramic Coating: Provides a protective layer against wear.
5. Quality Testing
Quality assurance is crucial. Each cylinder liner undergoes rigorous testing to ensure they meet the necessary industry standards. Tests may include:
- Dimensional Inspection: Verifying the accurate size and shape.
- Material Properties Testing: Ensuring the material meets required specifications.
- Performance Testing: Simulating operational conditions to gauge performance.
The Importance of Quality in Cylinder Liners
The quality of cylinder liners directly correlates to the overall performance of a diesel engine. Here are some reasons why high-quality manufacturing matters:
- Reduction in Maintenance Costs: High-quality liners lead to less frequent repairs and replacements.
- Improved Fuel Economy: Engines equipped with quality liners typically exhibit better fuel efficiency, which translates to cost savings.
- Environmental Benefits: Enhanced fuel efficiency also means lower emissions, supporting a greener environment.
Case Study: Excellence at Client-Diesel.com
At client-diesel.com, we pride ourselves on being a leading spare parts supplier in the diesel engine parts domain. Our cylinder liner factory exemplifies our commitment to quality and innovation. Here’s how we ensure our products stand out:
1. Advanced Technology
Our cylinder liner factory employs state-of-the-art machinery and technology to produce liners that meet the highest standards. Utilizing cutting-edge techniques such as CAD/CAM allows us to achieve precision in our products.
2. Skilled Workforce
We invest in our people. Our skilled workforce is not only experienced but also continuously trained in the latest manufacturing processes, ensuring every cylinder liner produced is of the best quality.
3. Customer-Centric Approach
Understanding our customers' unique needs drives our production process. Whether you're looking for customized solutions or bulk orders, we accommodate all requests with tailored service.
Future Trends in Cylinder Liner Manufacturing
The manufacturing of cylinder liners is evolving. Here are some future trends to watch:
- 3D Printing: As technology progresses, additive manufacturing may revolutionize how cylinder liners are produced, allowing for intricate designs and reduced waste.
- Smart Materials: The development of smart materials that can change properties under different conditions might lead to more dynamic engine performance.
- Automation: Increasing automation in manufacturing will streamline production processes, reducing costs and improving consistency.
Conclusion: The Road Ahead for Cylinder Liners
In conclusion, the role of a cylinder liner factory in the diesel engine parts supply chain cannot be overstated. High-quality cylinder liners are indispensable for optimal engine performance, longevity, and environmental sustainability. As manufacturers, suppliers, and users continue to push for advancements in technology and materials, the future of cylinder liner production looks promising.
At client-diesel.com, we remain committed to providing top-tier diesel engine parts while embracing innovation. Whether you are a manufacturer, supplier, or end user, partnering with us means investing in quality and reliability that stands the test of time.